Perfectly sharpened by the laser beam, woodworking tools are distinguished by longer life and greater durability. Thus, the choice of laser ablation directly translates into a more efficient production process. What distinguishes laser ablation?
What is laser ablation?
Laser ablation involves focusing a laser on a substrate to remove material on its surface. The amount we remove depends on the intensity, pulse length and wavelength of the laser, as well as the material itself. The laser pulse absorbs the area it is directed at, thus breaking up the chemical bonds. By using short, nanosecond (0,000,000,001) and ultra-short, picosecond (0,000,000,000,001) laser pulses of high quality, we remove material from the surface of the solid by means of sublimation, or evaporation.
The advantage of evaporation is that the surface of the workpiece is not heated and there is no thermal effect on the structure of the material. This makes the choice of laser ablation directly translate into a more efficient production process. Laser ablation is more accurate and efficient than traditional sharpening methods. We successfully use it to sharpen all diamond tools: heads, knives, cutters, drills and circular saws.
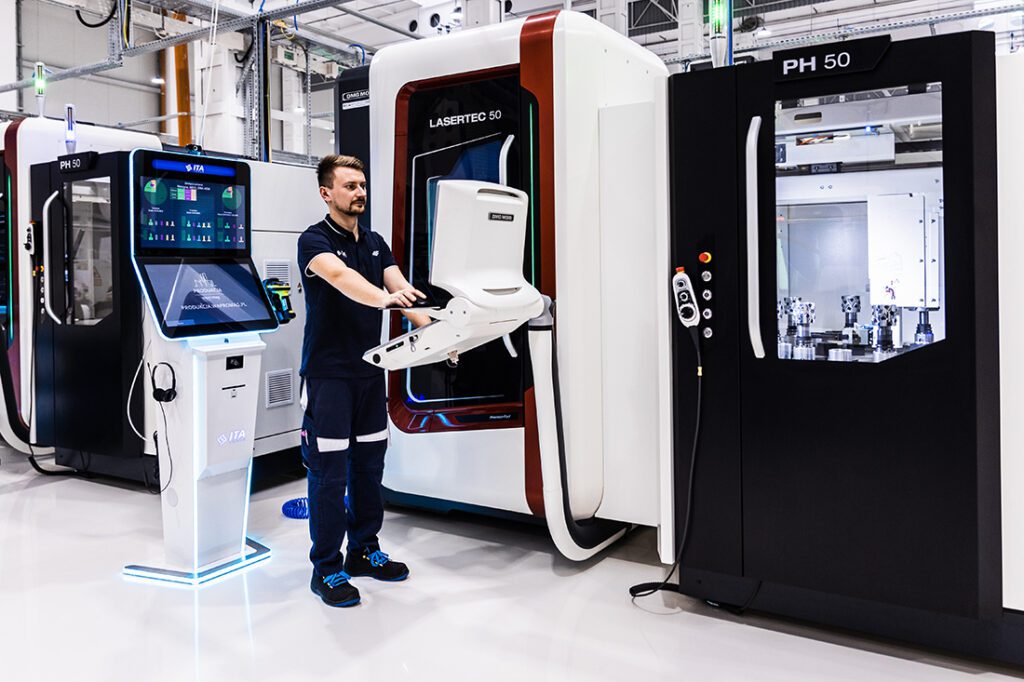
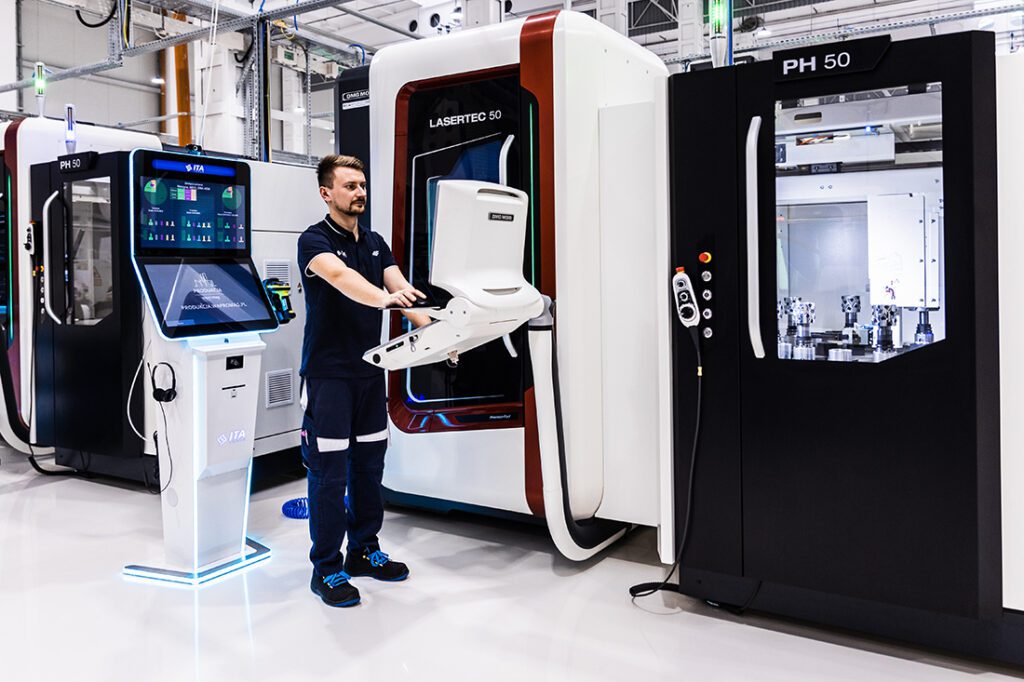
Laser ablation - benefits
PCD sharpening technology is provided by modern machines from the Japanese-German company DMG MORI. Full automation speeds up the sharpening process. Thanks to the possibility of sharpening the entire set in one cycle without the need to remove the blades, we maintain their even diameter. Laser ablation provides the ability to sharpen angles from 15 microns and maintain perfect precision even on the most complex profiles, such as for floor panel tools
It is also worth noting that, thanks to the specifics of its operation, laser ablation has an almost negligible negative impact on the environment. Thanks to all these aspects, it is safe to say that this method is revolutionising diamond tool sharpening in the woodworking industry.
Electro-erosion versus laser sharpening. Which to choose?
Electro-erosion is a widely known, classic method of sharpening diamond tools using an electric arc, disc or wire, or copper-tungsten electrode. Despite the excellent results of electro-erosion, the laser ablation method carries a number of advantages and significantly distinguishes itself from other sharpening methods. Why?
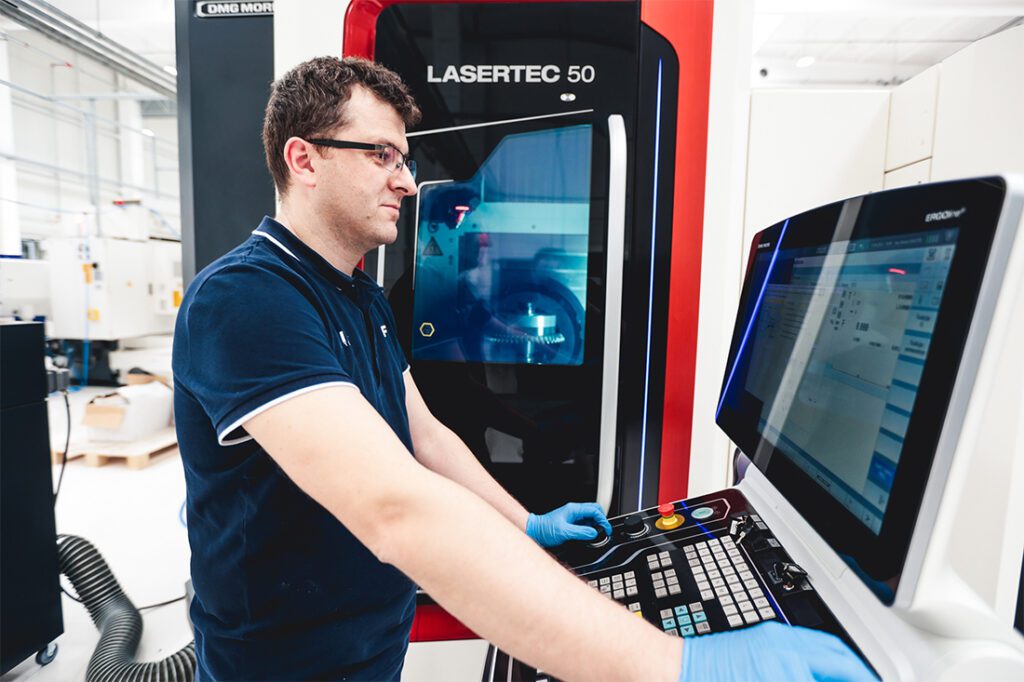
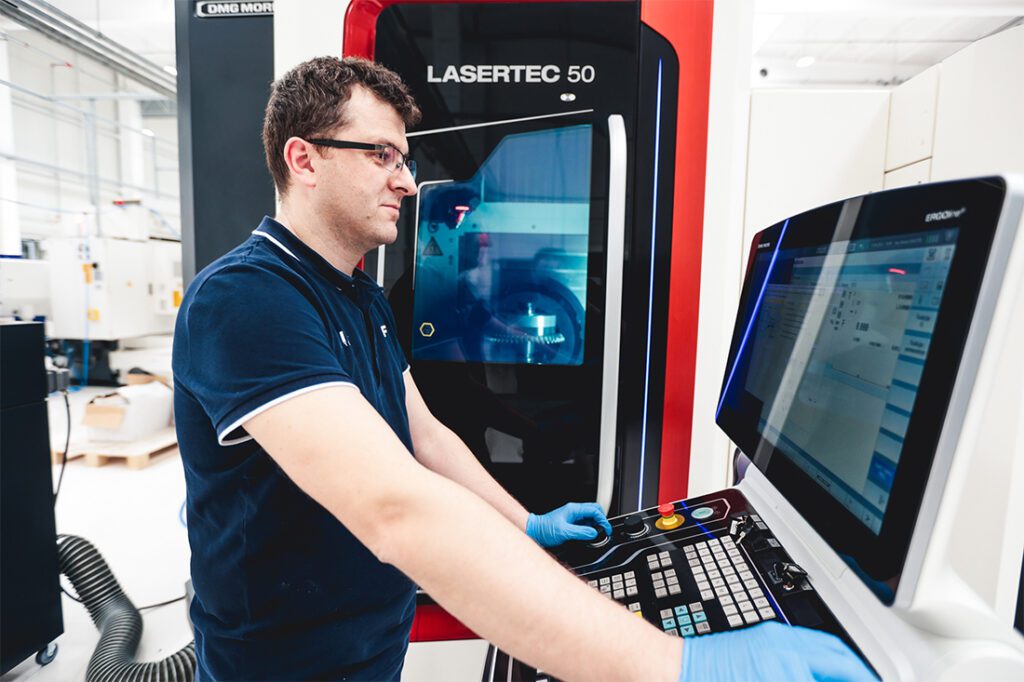
During traditional electrode sharpening, the sharpened edge has a not entirely even and consistent structure. This is because both the blade and the material around it are heated. The heated material melts and burns away, so a zone of damaged material is created by the heat wave.
Electroerosion makes it impossible to cut the diamond grains embedded in the bond of the diamond plate edge, because polycrystalline diamond (PKD) does not electroerode, as it only erodes the bond. In fact, the electric arc only causes the binder to melt and "tear out" through the rotary electrode the diamond grains. It is also impossible to sharpen chipbreakers with this technology, and the wire diameter required for this process makes it impossible to machine small radii. However, no edge is perfectly even. With laser beam sharpening, on the other hand, it is possible to sharpen profile tools, i.e. any shape can be given to the diamond plate.
Bet on new technologies
Despite the excellent results of electro-erosion, the laser ablation method provides significantly more benefits and differentiates itself from other sharpening methods. Compared to electro-erosion, the laser offers the possibility to sharpen tools with a chipbreaker and provides an excellent blade finish without splintering. This is because the laser cuts through the diamond grains. Furthermore, when using electro-erosion, the diameter of the electrodes makes it impossible to process small radii. For high quality, the sharpening process should be repeated 2-3 times.
As ITA TOOLS, we are a pioneer in laser ablation diamond tool sharpening technology and are the only company in Poland to offer this service to our customers. Contact us and see for yourself how an innovative tool sharpening method can affect your company's production.