Thanks to our state-of-the-art machinery, we offer the sharpening of all types of diamond tools: burrs, end mills, saws and undercutters while maintaining the original factory parameters. Check out our diamond tool sharpening service.
What makes diamond tools stand out?
Cutting tool blades used in the woodworking and furniture industries, commonly referred to as 'diamond tools', are created by sintering, under high pressure and at high temperature. They are formed from appropriately selected diamond grains of a specific gradation, with the addition of a metallic crystalliser, on a carbide substrate. The thickness of the layer containing the diamond grains does not usually exceed 0.6 mm. Suitably prepared blades are bonded to the tool body by brazing, thanks to the existence of a carbide backing layer.
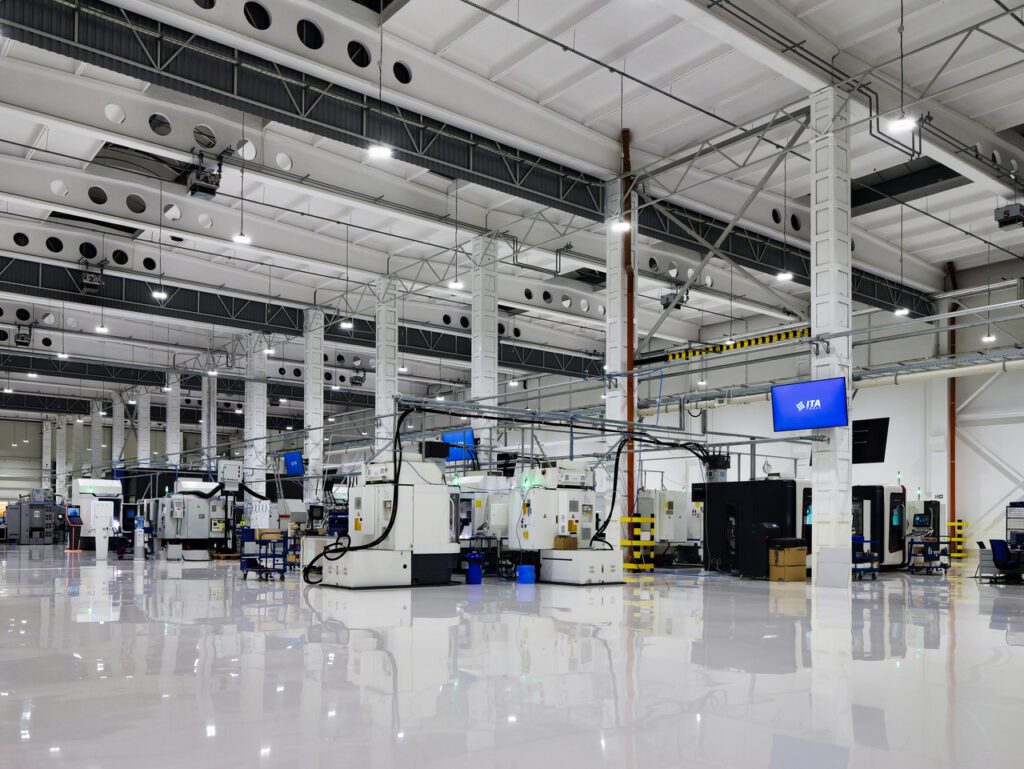
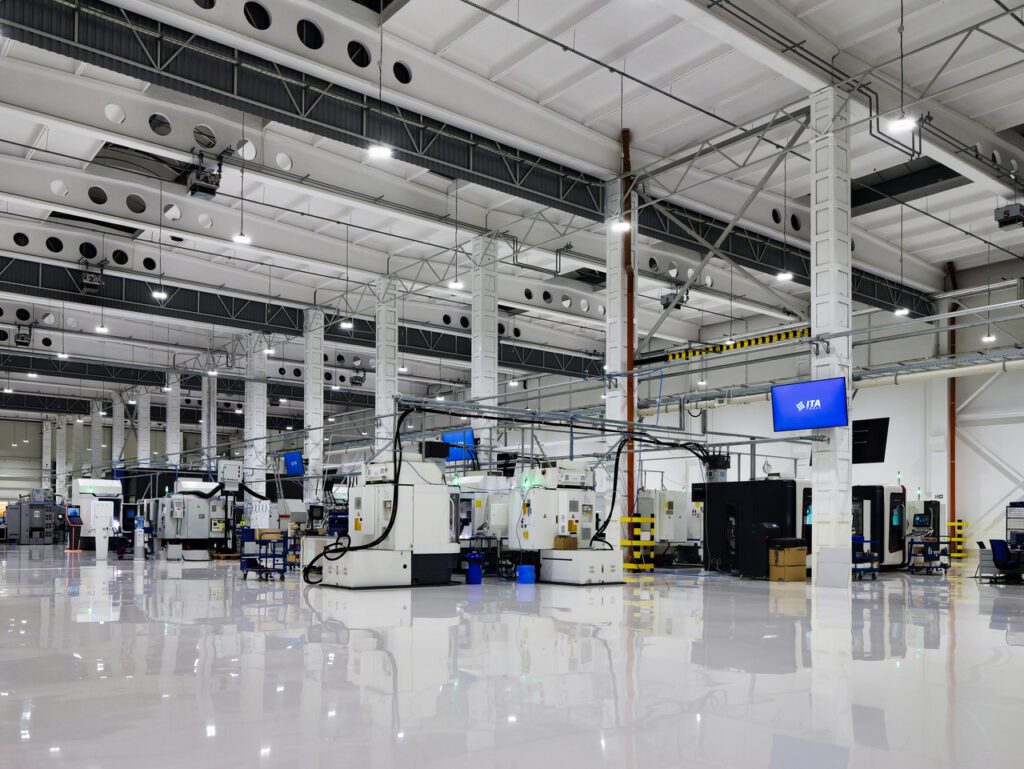
Polycrystalline diamonds are divided into fine, medium, and coarse diamonds, depending on the grain size used. Diamond tools are made as single-use and re-sharpening tools. Diamond tools are sharpened by electro-erosion or laser ablation. It consists of treating the blade using a current with suitably selected parameters. In practice, one electrode is the tool and the other is a copper-tungsten disc or wire. Laser ablation, on the other hand, involves using a laser beam to remove material on the blade surface.
The sharpening process is always preceded by cavity measurement, thorough cleaning and, if necessary, reconditioning of the tool. The measurement is carried out with an accuracy of 0.01 mm. In this way, the over-shooting required for sharpening can be kept to a minimum, extending the life of the tool.
In addition to diamond tools, we also accept carbide, VHM tools such as spiral cutters and hedgehog heads for servicing. We carry out servicing, including possible reconditioning, within three to five working days.
Tool sharpening - a service for your business
Diamond tools are increasingly popular in the woodworking industry. They are used for machining wood-based panels, especially for precision machining of furniture board. They are also excellent for processing plywood and hardwood for flooring.
The wood and furniture industries are our main focus, but services for the advertising industry, where films and materials such as HPL, Plexiglas and Corian are widely used, are also becoming increasingly popular.
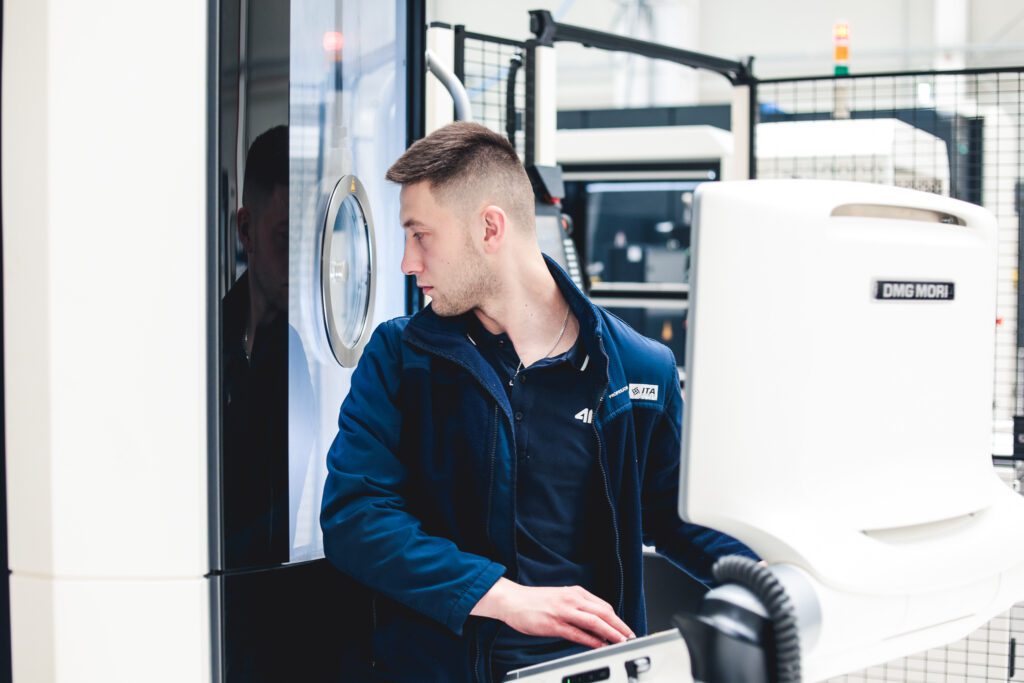
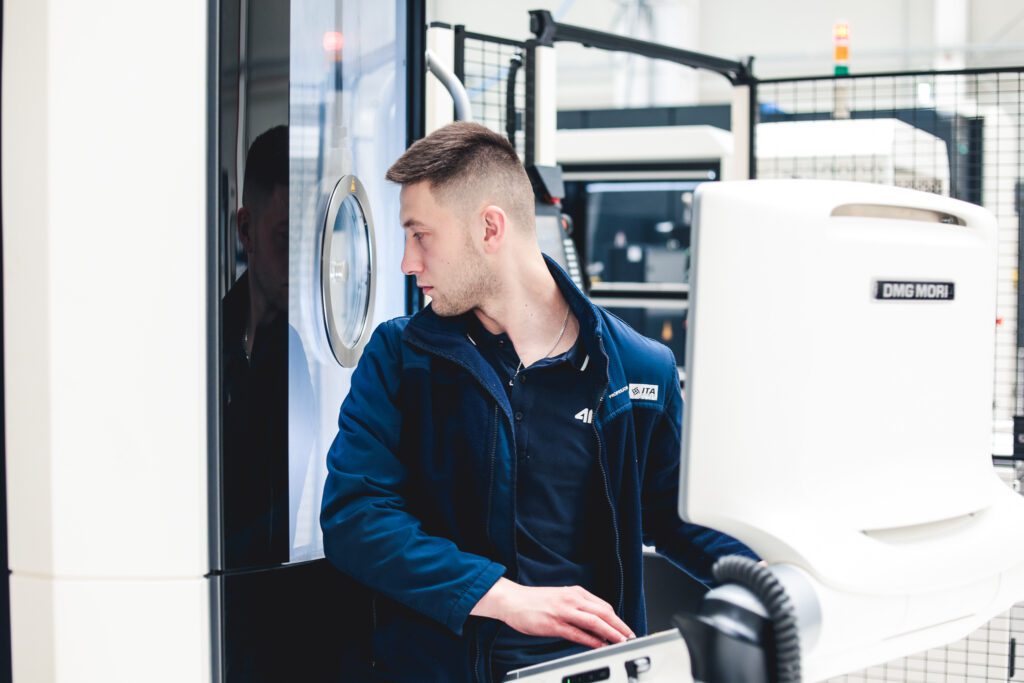
Numerically controlled machines, such as plotters, also use diamond tools. Our role is also to support customers in the selection and application of diamond tools to the material to be machined, in order to guarantee the best machining performance.
We carry out numerous tool tests at customers' premises and demonstrate the principles of correct operation. This allows us to extend tool life between sharpening, increase the number of sharpenings and improve the quality of the workpiece. We try to educate customers and inform them of what the tool is used for, what optimum parameters it should run on, what to look out for.
On our website we have described sharpening processbut we try to convey the main information during a direct visit to the customer.
Tool sharpening in Industry 4.0
An important part of sharpening diamond tools is the introduction of automation into the entire process. By marking the tools with a DataMatrix code, we can record each tool in our computer system and complete its service history. We know who received them, which operator performed the activity, how long the tool was sharpened and on which machine. This internal documentation and control process makes the implementers of the tool sharpening process fully accountable. It is immediately possible to establish at what stage the service is being carried out and what processes the tool was subjected to and when.
Additionally recorded for customers is the diameter of the tool before sharpening. This saves the tool as much as possible during sharpening in order to achieve the greatest possible number of sharpenings.
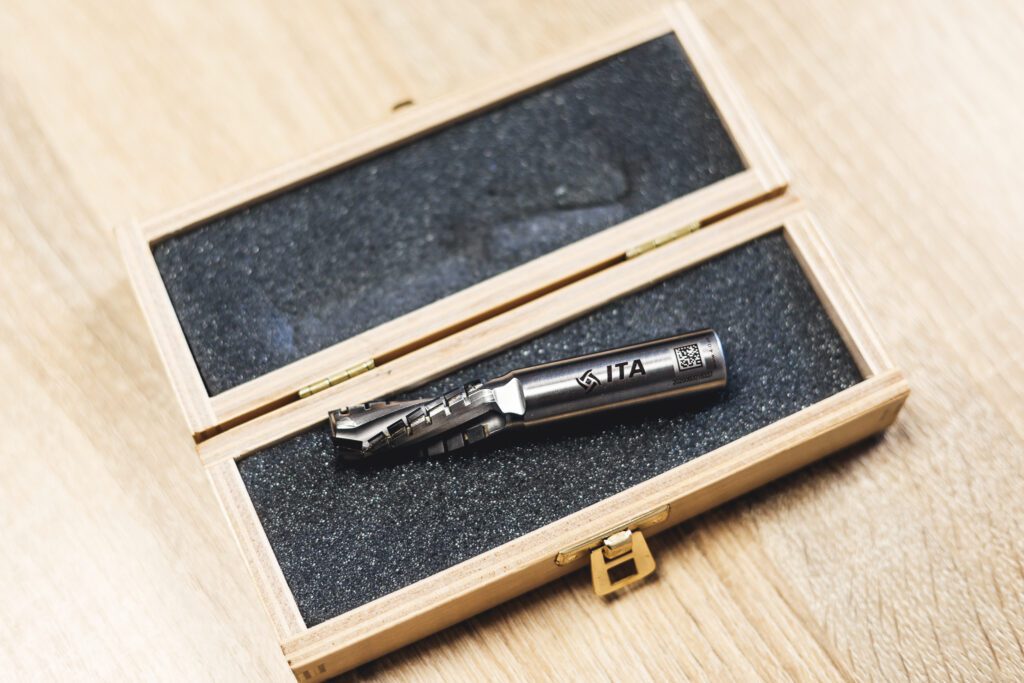
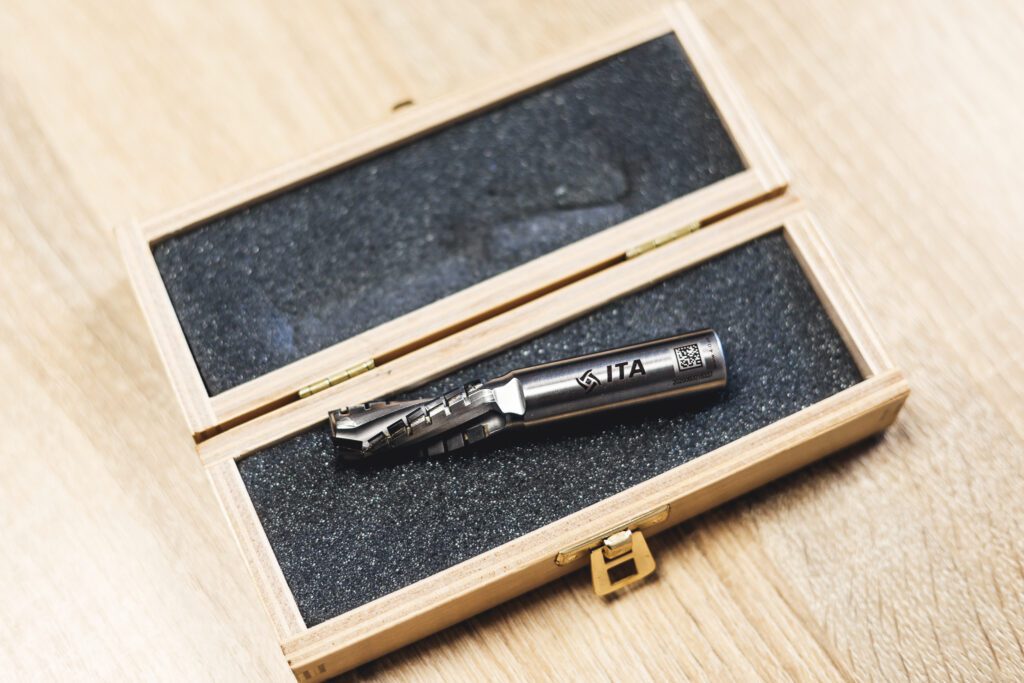
Specialised tool service
Diamond tools are characterised by high resistance to abrasion and overheating. The hardness of diamond inserts compared to carbide is significantly higher, which is important when machining wood-based materials. However, one of the most important advantages is precisely the high precision. PCD cutters are manufactured with a roughness of Ra ≤0.3 μm, which guarantees proper clamping on the chuck. It is the range of advantages of diamond tools that makes them increasingly popular.
As a diamond tool manufacturer, we know exactly how to conduct an effective service to restore your tool to its original condition and realise its full potential. Contact us to find out more about the service and the wide range of diamond tools at ITA TOOLS.